How FFF 3D Printing Technology Works
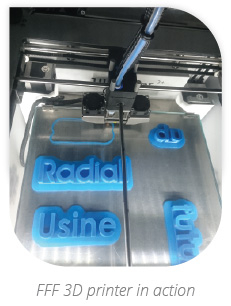
Fused Filament Fabrication (FFF) technology, also known as Fused Deposition Modeling (FDM), builds objects from the bottom up by layering plastic that’s heated in a moving extrusion head.
Comparing FFF to SLA
In a previous post, we detailed how SLA 3D printing technology works. SLA printers typically build models from top to bottom, and use a UV laser to cure photosensitive liquid resin into hardened plastic. The resin hardens where the laser hits the surface according to the 3D model supplied to the printer. The SLA printing process can be slower than FFF since it requires more preparation and post treatment, but it produces higher resolution models that are smoother and more precise due to the smaller size of the laser and the higher bonding force between resin layers.
Fused Filament Fabrication produces less accurate models compared to other types of printing technology, but the parts can be more robust and durable as they are not photosensitive. Due to its functionality and ease of use, these 3D printers are the most common type for home printing. FFF technology is also generally cheaper than other 3D print technologies.
Here’s how FFF 3D printing works
Using 3D model software, the user prepares the file for print by determining layer thickness, speed, and other factors. That model is then generated into a “.gcode” file that communicates to the 3D printer how to move and build the part. A material spool feeds plastic filament into a moving extrusion head that heats and melts the plastic, sending it through the nozzle onto the build platform where is lays the plastic along the correct design path coordinates. As the head deposits the plastic filament, each layer is bonded to the previous one. This process continues until the model is complete. The building platform is heated to improve bonding and prevent deformation of the parts.