What You Didn’t Know About Cleanrooms
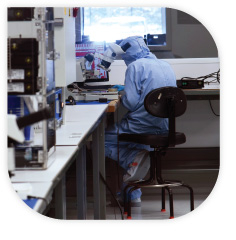
Cleanrooms are controlled environments with very low levels of pollutants to ensure manufacturing processes aren’t adversely impacted by small particles. Radiall uses cleanrooms to develop and manufacture certain fiber optic and active products such as D-Lightsys transceivers, where small particles would adversely affect the manufacturing process.
A quick refresher on FO technology
Fiber optic technology uses microscopic stands of glass to transmit data. Data electrons generated by computers or other devices are converted into bits of light called photons, carried over long distances through strands of glass, and ultimately converted back into electrons, all at lighting fast speeds. The light carrying data is emitted through strands with diameters less than the width of a human hair with the help of a variety of optoelectronic components and photonic devices that generate, modify, guide, and detect the optical signal.
Active fiber optic components, such as D-Lightsys, require semiconductor laser technology to provide the light in the fiber optic strand, meaning they require the integration of electronics and wiring. Passive components differ from active components because they don’t require power or electronics. They are components that only send the light signals traveling through the optical fiber. These components are assembled into packages that couples the light into and out of fiber optic cable.
Aligning and positioning optical fibers and components requires technical skill, accuracy, and submicron adjustments. Dirt, particles, and other air contaminants can degrade the signal quality of fiber and cause increased attenuation.
The reliability and performance of fiber optic technology is dependent, in large part, on the light signal passing through the core of the fiber without interference. In the manufacturing process, even the smallest particle contamination can result in light transmission loss, so most FO products are assembled in cleanroom environments. Here are 15 facts you didn’t know related to cleanrooms.
- 1. A human hair is 100 microns. The smallest size visible to the human eye is 50 microns. The size of particles counted in clean rooms is 0.5 microns.
- 2. Most particles are too small to be seen without aid, and their small size results in electrostatic bonding to surfaces.
- 3. People account for roughly 75% of contamination sources in clean rooms and the remaining 25% comes from other sources such as ventilation, room structure, and equipment.
- 4. The particles generated by a person just sitting or standing motionless is 100,000 particles sized 0.3 microns or larger.
- 5. Clean rooms are maintained at higher pressure than the surrounding area because if there are any leaks, air will leak out of the room instead of unfiltered air going in.
- 6. An airlock is a small chamber which permits the passage of people and objects between the pressure positive vessel and the surrounding area.
- 7. The airlock has two airtight doors that don’t open simultaneously to minimize the change of pressure in the vessel and the loss of air from it.
- 8. The High-Efficiency Particulate Air (HEPA) filter traps 99.97% of airborne particles 0.3 microns and larger.
- 9. The Ultra-Low Penetration Air (ULPA) filter traps 99.99% of particles 0.12 microns and larger.
- 10. Clean rooms are classified according to the number and size of particles permitted per volume of air.
- 11. Large number classifications like “class 100” or “class 1000” denote the number of particles of size 0.5 μm or larger permitted per cubic foot or air.
- 12. Small number classifications refer to ISO 14644-1 standards, which specify the decimal logarithm of the number of particles 0.1 μm or larger permitted per cubic meter of air.
- 13. An ISO class 5 cleanroom has at most 100,000 particles per cubic meter of air.
- 14. The ambient air outside in a typical urban environment may contain as many as 35,000,000 particles per cubic meter, 0.5 μm and larger in diameter, corresponding to an ISO 9 cleanroom.
- 15. Proper gowning order for entering the clean room includes using a face mask, hair cover, hood, coverall over hood base, boots over coveralls, safety glasses, and gloves.